In this post, I will perform an S-Beam Crash, an example from the RADIOSS guide.
The description of RADIOSS is as follows
An S-beam is crushed at an initial rate of 5 m/s against a rigid wall. The section is an empty square-shaped tube (each side measuring 80 mm).
The thickness is 1.5 mm. The tube is made of steel, and plasticity is considered, but not failure.
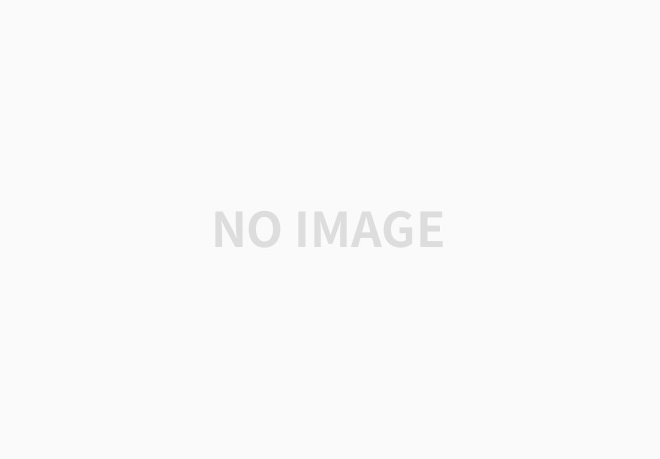
Material Properties
Young's modulus : 199355MPa
Poisson's ratio : 0.3
Density : 7.9e-3g/mm^3
Yield stress : 185.4MPa
Hardening parameter : 540MPa
Hardening exponent : 0.32
Maximum stress : 336.6MPa
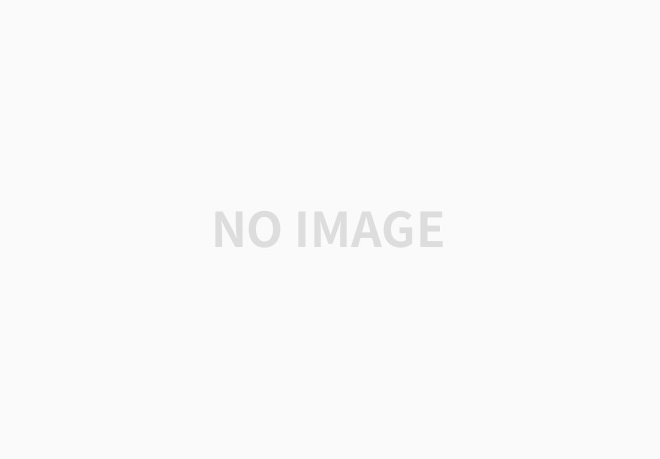
As in the previous post, I'll create the model in HyperMesh and import it in HyperCrash.
Model - Material
Create New - Elasto plastic - Johnson Cook
RHO_I : 7.9e-3
E : 199355
Nu : 0.3
a : 185
b : 540
n : 0.32
SIG_max0 : 336.6
Property
Thick : 1.5
Create a rigid element.
Mesh Editing - Rigid Body
MASS : 5000
select the left side
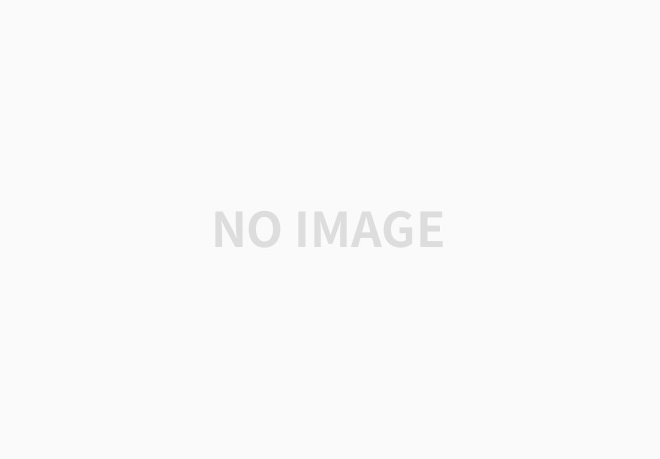
Create boundary condition
Check all dof
Gnod_id : select the right side
save
Create new boundary condition
Check all dof except TX and TY
Gnod_id : select a rigid node
Save and Close
Speed setting
LoadCase - Imposed - Imposed Velocity
Dir : X
funct_IDT : Define Function
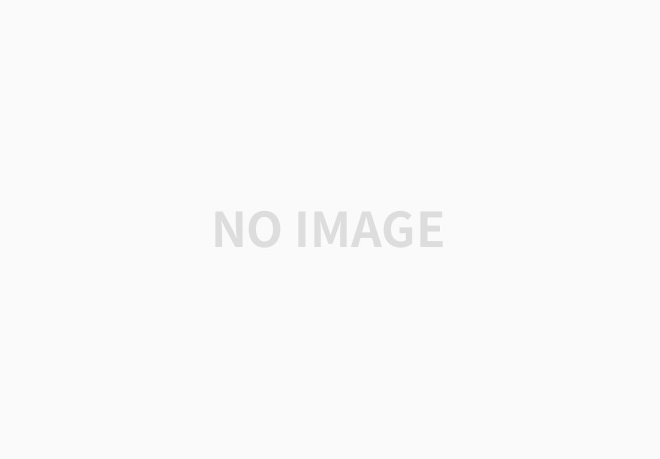
grnod_ID : select a rigid node
save and close
contact condition
The contact condition doesn't give much information, so I only checked the self impact.
Model - Control Card
RUN_NAME_NUMBER_LETTER
Run Number : 1
DT_STOP : 30.01
The other values are the same as in the previous post.
File - Export -RADIOSS -save model
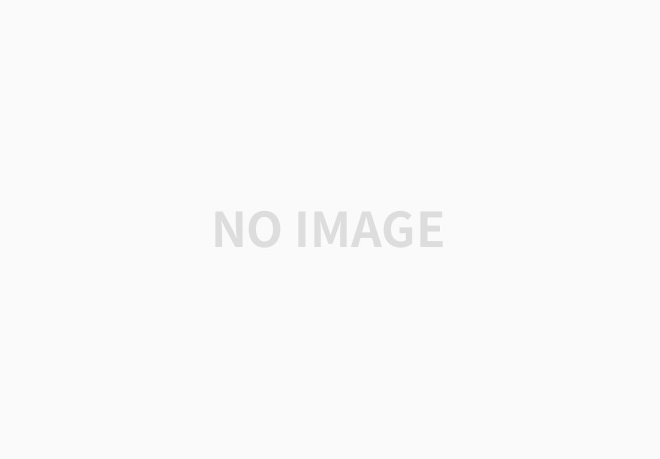
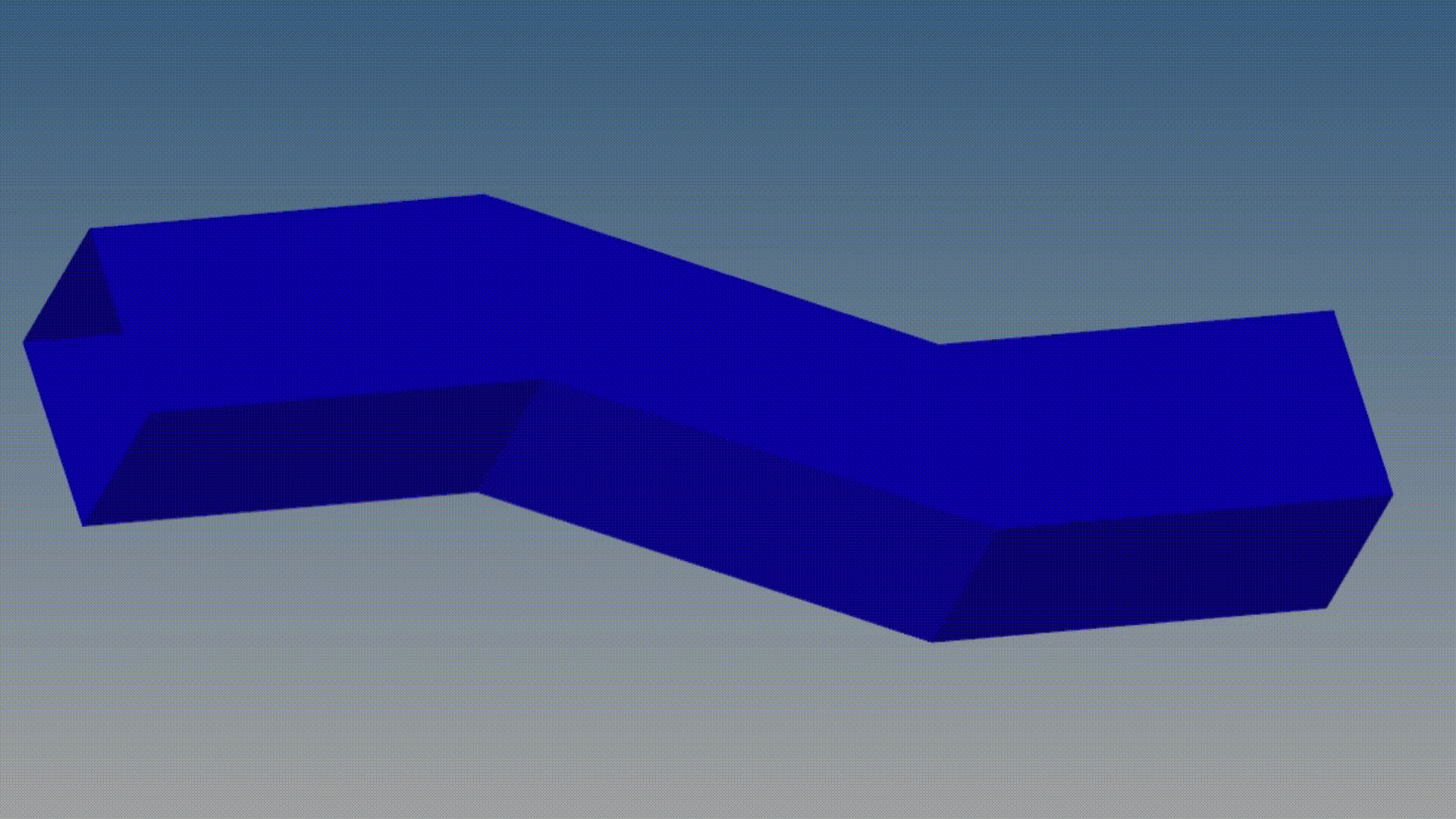
The results are shown above, and I'll explore them in more detail in the next post.
'Structural Analysis > OptiStruct' 카테고리의 다른 글
13_Pendulums (0) | 2023.12.13 |
---|---|
12_S-Beam Crash (0) | 2023.12.12 |
10_Impact analysis (0) | 2023.12.10 |
9_Contact analysis (0) | 2023.12.09 |
5_Buckling analysis (2) | 2023.12.05 |